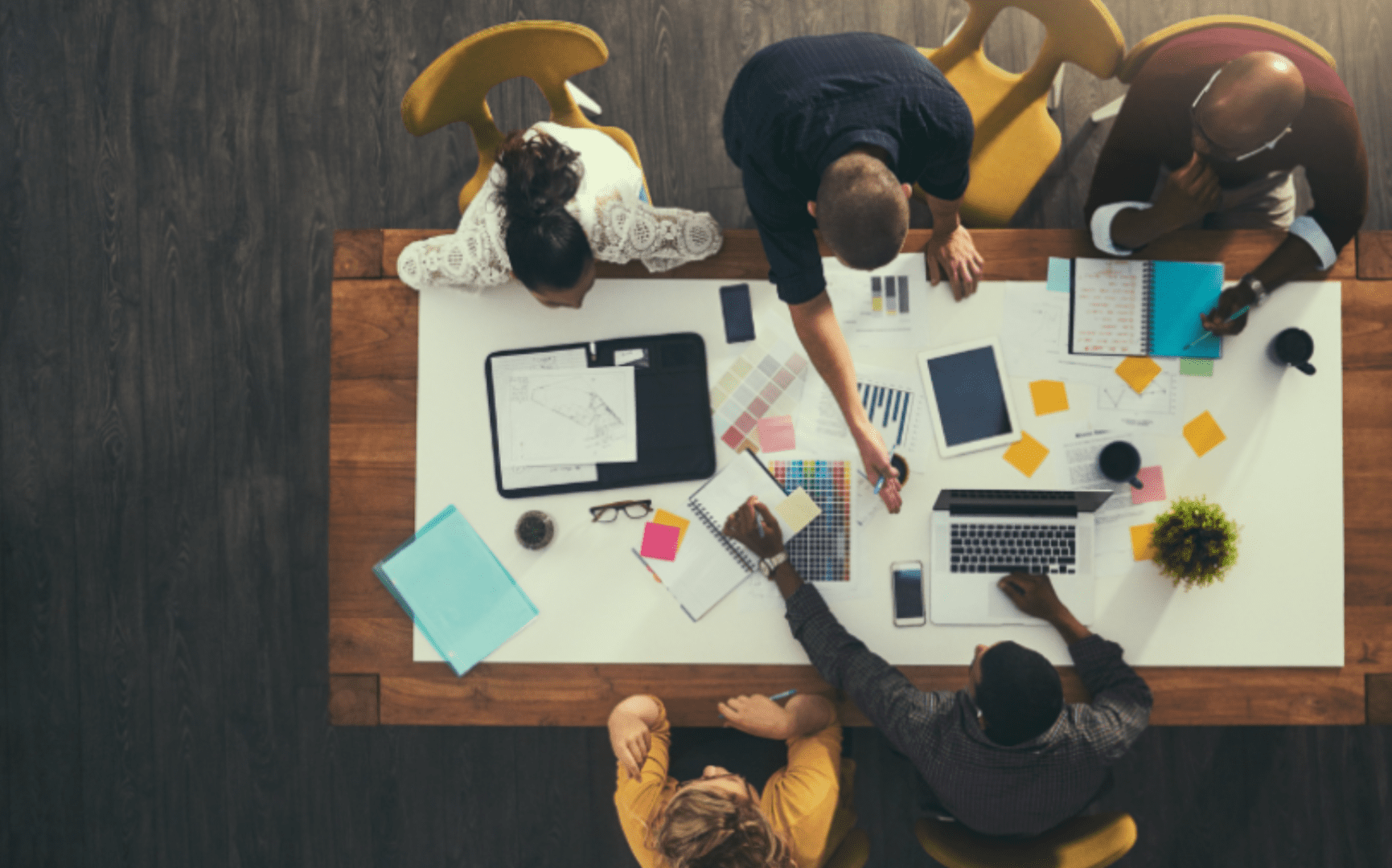
The Connection: February 2025 Issue #66
Companies are constantly looking for ways to streamline operations, reduce costs, and increase efficiency. One method that has gained significant attention is Lean Management. This approach is about doing more with less by minimizing waste and improving processes.
Let’s dive into how Lean principles can transform your business operations, and practical examples in manufacturing and other industries.
What Are Lean Principles?
Lean principles originated from Toyota’s production system and are widely used in various industries today. The core idea is to maximize value by minimizing waste. Waste can be time, materials, effort, or resources that don’t add value to the customer. Lean aims to create efficient processes that deliver value to the customer with minimal resources.
There are five key principles of Lean:
- Value: Understand what your customers truly value and focus on delivering that.
- Value Stream: Identify all the steps in your processes and eliminate anything that doesn’t add value.
- Flow: Ensure that the process flows smoothly without delays or interruptions.
- Pull: Only produce what is needed when it’s needed to avoid overproduction.
- Perfection: Continuously improve processes to strive for perfection.
Lean Principles in Supply Chain Management
Supply chain management (SCM) involves overseeing the flow of goods and services from the point of origin to the point of consumption. Lean principles can be extremely beneficial in supply chain management as they help reduce inefficiencies, lower costs, and improve customer satisfaction. Here’s how Lean can be applied in SCM:
- Eliminate Waste: Waste in the supply chain could be excess inventory, unnecessary movement of goods, or delays in transportation. Businesses can make their supply chain more efficient by identifying and eliminating these wasteful activities.
- Continuous Improvement: Lean encourages a culture of continuous improvement. In the supply chain, this means regularly evaluating suppliers, logistics, and production processes to find ways to enhance performance.
Lean Mapping
Lean mapping is a visual tool for identifying and understanding the flow of materials, information, and processes within an organization. It’s often referred to as Value Stream Mapping (VSM). In lean mapping, you create a diagram that shows the steps in a process, identifying where waste occurs. By using this map, you can pinpoint areas for improvement.
- Current State Map: This shows the current process flow. It helps to identify inefficiencies or delays in the process.
- Future State Map: After identifying the issues, a future state map shows the ideal, streamlined process.
- Action Plan: Based on the future state map, you can create an action plan to make improvements and eliminate waste.
It is especially useful in complex operations, such as supply chains or manufacturing, where it isn’t easy to see the full process from start to finish.
Lean Management Examples
Lean management principles can be applied in various industries. Let’s explore some practical examples:
- Lean Manufacturing:
- Toyota is the birthplace of Lean manufacturing. The company uses Lean principles like JIT and continuous improvement to produce high-quality vehicles efficiently. By reducing inventory levels and minimizing waiting times between production stages, Toyota can keep costs low while meeting customer demand.
- Lean in Healthcare:
- Many hospitals apply Lean principles to improve patient care and reduce waste. For example, reducing the time spent waiting for procedures or tests. Lean management helps streamline the process, allowing quicker response times and better resource utilization.
- Lean in Service Industries:
- Call centres often use Lean to improve customer service and response times. Call centres can provide quicker, more efficient service by analyzing call flow, identifying unnecessary steps, and focusing on key customer needs.
Process Lean Management
It aims to continuously evaluate and improve internal processes to eliminate waste and enhance value. This involves:
- Process Mapping: Mapping out current workflows and identifying where inefficiencies lie.
- Root Cause Analysis: Using tools like the 5 Whys or Fishbone Diagrams to find the root cause of problems and eliminate them.
- Kaizen: A Japanese term for “continuous improvement.” Kaizen emphasizes small, incremental changes rather than large, disruptive ones.
- Standardized Work: Ensuring that processes are standardized to maintain consistency and efficiency.
Conclusion
Implementing Lean principles can transform business operations. By using tools like Lean mapping and focusing on the core principles, you can build a foundation for sustainable growth and operational excellence.