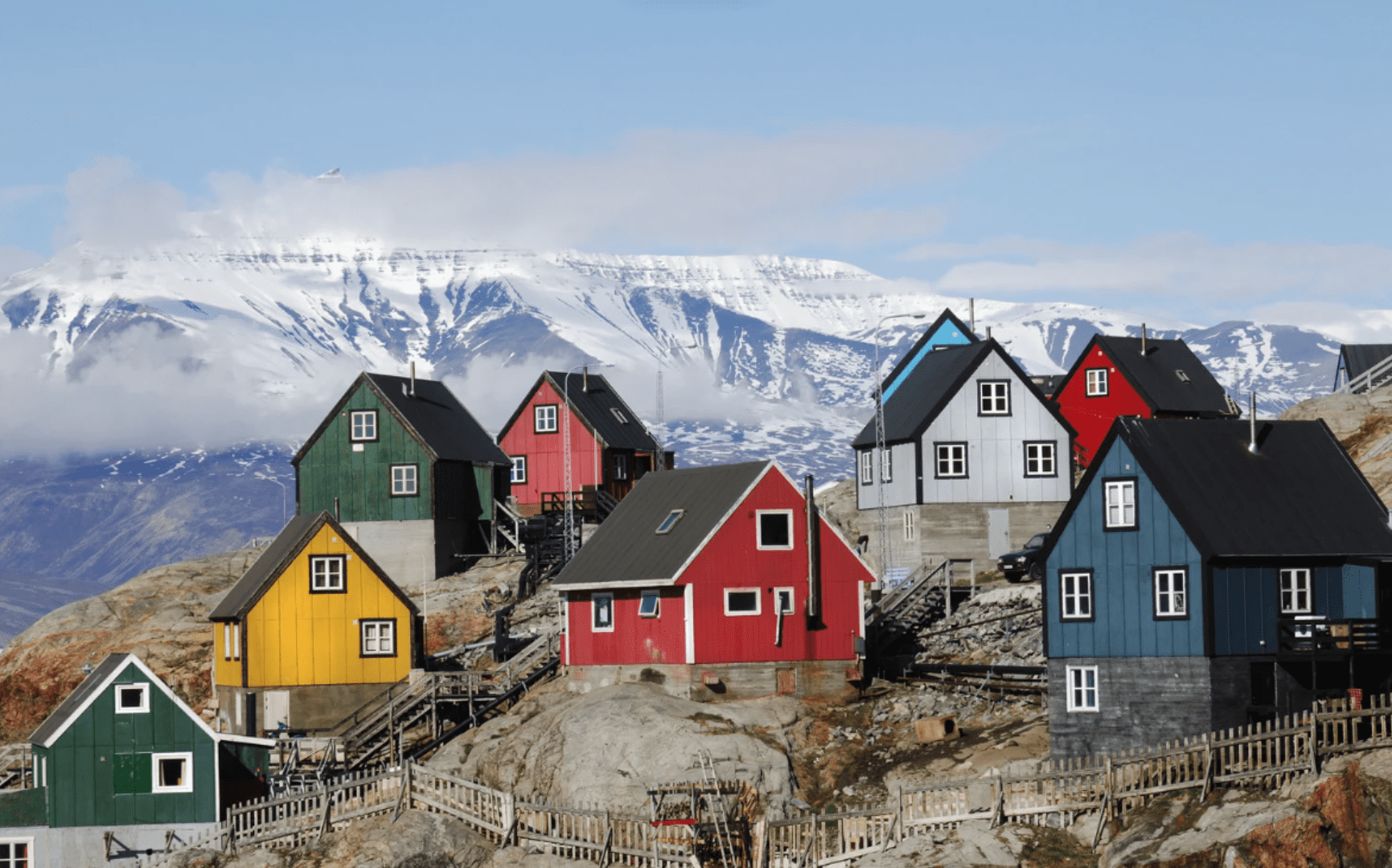
The Connection: April 2025 Issue #72
Prefabrication and modular construction are revolutionizing the building industry. In the Midwest, where demand for efficient and affordable housing is growing, prefabrication offers a faster, cost-effective, and high-quality alternative to traditional construction.
By optimizing business processes, companies can improve efficiency, reduce waste, and enhance profitability.
This article explores how supply chain management, construction management, and digital transformation contribute to the success of modular and prefab home manufacturing.
What Are Modular and Prefabricated Homes?
Factories build modular and prefabricated homes in sections and then transport them to the site for assembly. Unlike traditional homes constructed on-site from the ground up, this process controls the environment, reducing delays from weather and labor shortages. Prefabricated homes range from simple, small units to large, multi-story buildings.
Business Process Optimization in Prefabrication
Business process optimization (BPO) helps streamline operations, reduce costs, and improve the quality of prefab homes. Key areas of improvement include supply chain management, construction management, and digital transformation.
1. Supply Chain Management
Supply chain efficiency is crucial for prefab manufacturers. Managing the supply of raw materials, coordinating logistics, and reducing waste is vital to maintaining a steady production flow.
- Material Sourcing: Prefab manufacturers must establish reliable relationships with suppliers to ensure a steady flow of materials. Bulk purchasing and just-in-time inventory management help reduce costs and storage issues.
- Logistics Coordination: Efficient transportation of prefab sections requires detailed planning. Late or damaged deliveries can lead to costly project delays.
- Sustainability Practices: Using recycled materials and reducing waste can lower costs and appeal to environmentally conscious buyers.
2. Construction Management
Effective construction management is necessary to ensure quality control and timely project completion. In prefabrication, this means overseeing the manufacturing process in the factory and coordinating on-site assembly.
- Standardized Processes: Setting up clear production guidelines ensures uniformity in design and quality.
- Workforce Training: Employees must handle specialized machinery and follow strict safety regulations.
- On-Site Coordination: Once the prefab units are transported to the site, teams must work efficiently to complete assembly with minimal disruptions.
3. Digital Transformation in Prefabrication
Digital transformation in the prefabrication streamlines design, manufacturing, and assembly through AI, automation, and data analytics. It enhances efficiency, reduces waste, and accelerates project timelines for smarter construction.
- Building Information Modeling (BIM): BIM software allows architects, engineers, and builders to collaborate on digital models, reducing errors and improving efficiency.
- Automation and Robotics: Automated systems and robotic arms help speed production, reduce labour costs, and improve accuracy.
- Smart Manufacturing: Using IoT (Internet of Things) devices in factories allows real-time production monitoring, identifying bottlenecks before they cause delays.
Benefits of Prefabrication in the Midwest
The Midwest is seeing a surge in prefabricated construction, driven by its cost-effectiveness, sustainability, and ability to meet growing housing demands efficiently.
- Cost Savings:
Factory-built homes significantly lower labor costs, minimize material waste, and allow for bulk purchasing of materials, making construction more affordable.
- Faster Construction:
With off-site manufacturing and on-site assembly happening simultaneously, projects can be completed in weeks instead of months, helping to address housing shortages and meet demand quickly.
- Weather Protection:
Since the majority of the construction process takes place indoors, prefab homes are shielded from extreme weather conditions, reducing delays and material damage caused by snow, rain, or storms.
- Energy Efficiency:
Many prefab homes incorporate high-performance insulation, energy-efficient windows, and sustainable building materials, leading to lower energy consumption and reduced long-term costs for homeowners.
Challenges and Solutions
Despite its advantages, prefab manufacturing faces challenges such as transportation logistics, limited design flexibility, and regulatory hurdles.
- Transportation Costs: Prefab sections must be transported carefully to prevent damage. Investing in better packaging and secure transportation can minimize risks.
- Design Limitations: Some buyers may prefer custom designs. Offering modular customization options can attract more customers.
- Regulatory Compliance: Prefab buildings must meet local building codes. Staying updated with regulations and working closely with policymakers can help avoid legal issues.
Conclusion
Prefabrication is transforming the construction industry in the Midwest, offering an efficient and sustainable solution for housing needs. By optimizing business processes in supply chain management, construction management, and digital transformation, prefab manufacturers can enhance productivity and profitability. As technology advances, the future of modular and prefab homes looks promising, making them a key player in modern construction.